From smaller, more irregular packages, to new market segments like micro-fulfillment automation, the change driven by e-commerce is reflected in the conveyor and sortation market. Add in the need to offer systems that are faster to put in and more adaptable over time, and you see multiple reasons for these trends.
Conveyor and sortation systems remain at the heart of automated material flow in many warehouses. While guided vehicles and autonomous mobile robots (AMRs) are alternative means of automated transport, and semi-automated systems like pick to light can do sortation. New market segments and niche industries that are continuing to grow are adding to the need of quick, modular, reliable materials handling options.
With the growth of e-commerce and faster delivery cycles expected for store replenishment, Distribution Centers (DCs) continue to deploy conveyor and sortation systems at an accelerated rate. According to a recent analyst report from Technavio, the global conveyor and sortation market is expected to grow at compound annual growth rate of more than 5% through 2024.
Conveyor and sortation solutions are changing, however, to adapt to new types of packages, processes and market niches some vendors are adapting to using mobile robots with pallet lift trays or other attachments on top to mimic the functionality of fixed sortation. While some conveyor suppliers also have products that address emerging niches such as micro-fulfillment or high throughput sortation centers.
E-commerce growth is the lynchpin to the recent conveyor, sortation and materials handling trends. All those small consumer orders are often shipped in polybags, padded envelopes or other small and lightweight packages that present challenges different from corrugated boxes. Here are a few top trends and insights from conveyor and sortation options.
Plastic – Polybag Problems
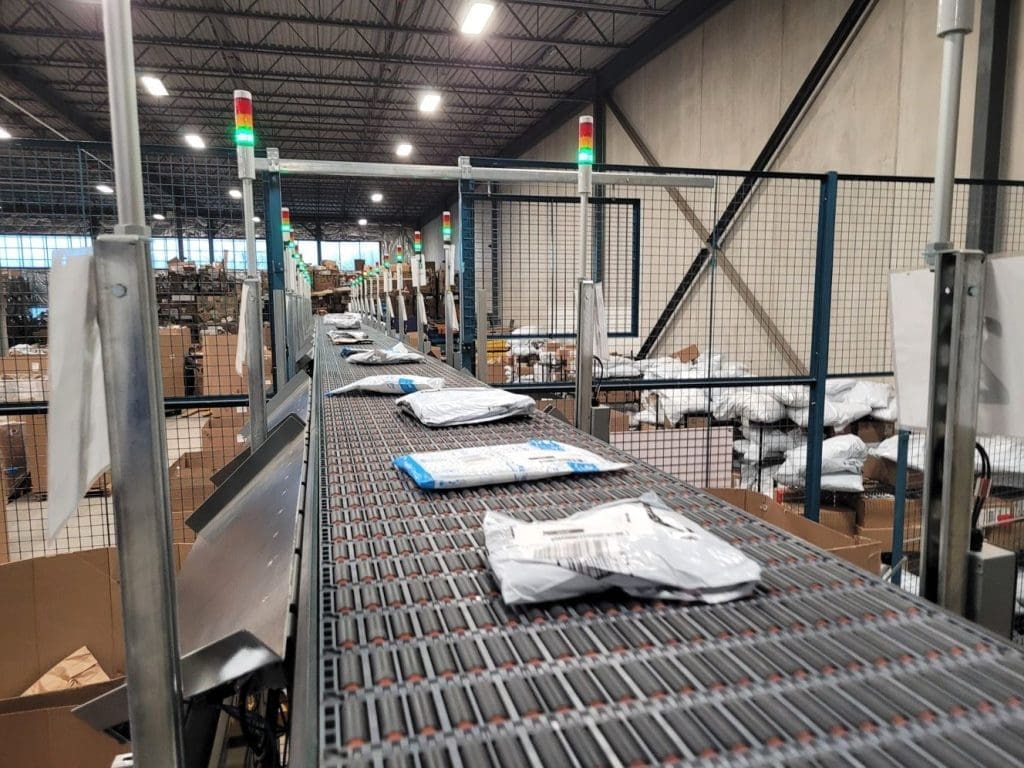
With e-commerce driving greater use of polybags, conveyor and sortation systems may have to be changed or adapted to handle these items. According to product Tim Kraus, manager with Intralox, the issue with polybags is that unlike traditional corrugated cartons, they don’t have uniform, flat bottoms, and second, the same bag size can hold items that are significantly different in weight and shape.
“With boxes and with totes that might hold several orders, conveying is pretty easy because boxes and totes have flat bottoms that are easy to handle and the edges are easy to detect,” says Kraus. “That makes it easier to control the motion. By contrast, with a polybag, it’s much more difficult to control and precisely predict the path of the items, because you are not just handling a bag, you are handling whatever is inside plus new catch points created by the bag itself.”
The same sized polybag, Kraus points out, could be used to ship a relatively small but heavy hammer, or a lightweight replacement O-ring or a sweater. “In singulated polybag flow, it becomes important that you have good transitions from conveyor to conveyor, rather than large gaps from one conveyor to the next,” he says. “This can help avoid problems with polybags getting jammed or losing their tracking location in the software. In bulk polybag flow, it’s important to make sure you’ve eliminated any catch point, and to use waterfall transitions instead of completely level transitions.”
If a DC is doing more e-commerce shipping of polybags, it’s wise to revisit rougher transitions and maybe put in different transitions to be able to deal with smaller items, adds Kraus. With singulation also being difficult with polybags, adds Kraus, some facilities are moving from singulated flow they used for larger cartons to a bulk flow for polybags or mixed package types, with sortation done later. Going to bulk flow allows for use of a conveyor to move from an order packing area of the building to shipping.
With new systems and improvements, it may be best to opt for sorters well suited for small items. Intralox offers a type of belt it calls Activated Roller Belt, or ARB. This type of belt, explains Kraus, uses many small rollers that can be activated to change direction of the goods being conveyed, making it a good type of belt for handling polybags or other lightweight items for more complex functions like bulk sorting, singulation and single-item sorting.
“We use the ARB technology in many ways, but it’s ideal for polybags because it has many small points of contact,” Kraus says.
Belt to Box – Telescoping Conveyors

One the impacts of doing more e-commerce fulfillment at DCs is that items like parcels and cartons might be loose loaded into trailers or vans rather than palletized. This can mean plenty of short trips by workers to get such goods loaded or unloaded under a manual method.
Telescoping conveyor comes in different variations with the idea being “bring the belt to the box” to eliminate most of the walking, carrying and other small movements in handling loose loaded cargo. With the touch of a button, a telescoping conveyor can be extended by a worker into a trailer, so the conveyor’s belt brings goods right near the point of work, and when unloading, positions the conveyor close to the items that need unloading.
With telescoping conveyor, we’re able to minimize the number of steps and the overall labor effort involved with loading and unloading loose cargo. E-commerce is really starting to increase the need for more automation, including telescoping conveyors and other powered conveyors.
Another area benefit with telescoping conveyors is that the increased efficiencies involved may allow one worker to handle a task, rather than a team of workers. If you used to have two people load or unload a trailer, telescoping conveyor can make it possible to do the task with one person. With increased safety measures worldwide, this helps reduce risk by reducing the number of people going in and out of a trailer.
Small but Mighty – Micro-Fulfillment Centers
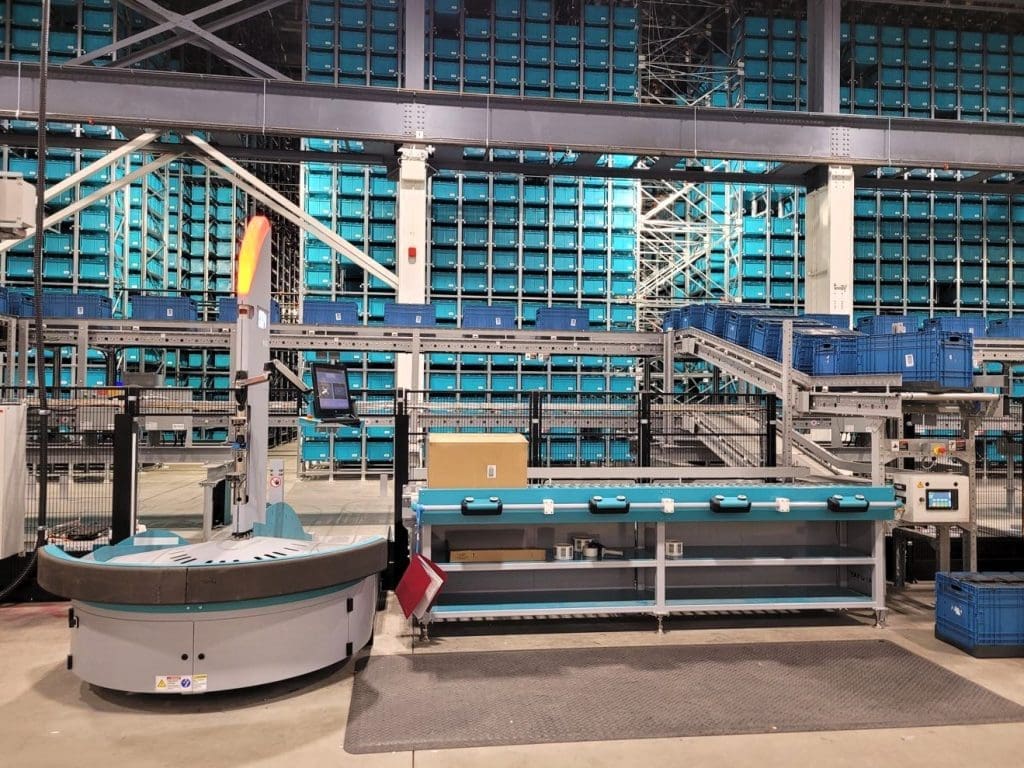
The growth in e-commerce and consumer interest in curbside or in-store pickup has some grocers and retailers experimenting with micro-fulfillment, which involves putting automated storage and order picking solutions into stores or dark stores. The idea is that by having many automated points of distribution close to customer concentrations, a retailer can excel at fulfillment speed and efficiency.
With some micro-fulfillment solutions incorporating conveyors and some using other conveying means, there needs to be a conveyor with strong data communication, higher speed capabilities, modularity, and precise positioning characteristics.
Micro-fulfillment centers tend to operate at higher throughput and want the flexibility of being able to repurpose the conveyor in different configurations as their needs change. Some of the more advanced micro-fulfillment centers utilize robotic interaction that requires precise product handling for robot collaboration.
Overall, micro-fulfillment center automation solutions need to be fast and reliable to make orders available quickly for consumers and provide them with a superior level of service. Because of these needs, precise positioning of totes and data feedback characteristics will be needed from conveyor used as part of this growing niche.
Contact us today to integrate a modular, adaptable, and efficient sortation system or distribution center in your warehouse today.
Comments are closed