The unprecedented disruption experienced across industries in 2020 magnified the need for supply chains to be more resilient, agile, and crisis-proof. To date, the disruption is still ongoing. Companies are still working hard to address COVID-related material shortages and the world’s transportation networks are struggling to keep up with the demand.
Fortunately, even in the midst of an economic recession due to the pandemic, more advanced technologies have proven themselves useful for companies to gain a competitive advantage. Automating key elements in their supply chains has helped companies expedite processes that are usually time-consuming. For most, automation has also helped with the imperative need for social distancing in workplaces.
Supply chains benefit largely from automation and we’re seeing retailers, manufacturers, and logistics providers increasingly adopting some form of automation to address their business needs mid- and post-pandemic. Will your business be making the shift to automation this year, too?
What Is Supply Chain Automation?

Supply chain automation refers to systematizing part or all of a complex workflow to simplify and improve processes using digital technologies such as:
- artificial intelligence (AI),
- machine learning (ML),
- Robotic Process Automation (RPA), and
- Optical Character Recognition (OCR).
Automating the supply chain aims to lower the operational cost of delivering a product or service. It ultimately reduces manual effort while increasing productivity, efficiency, and productivity. Despite being a significantly huge investment, most companies that adopt it see it as a huge advantage in the long run.
Supply Chain Automation in Action
Supply chain networks are rife with redundant and process-oriented tasks that are highly prone to errors. These are often seen in manual documentation, picking and stocking, and shipping and receiving. With supply chain automation, businesses are able to identify these repetitive tasks and find ways to simplify them using technologies that are widely available in the market.
Here’s how automation can be applied effectively in the supply chain:
- Back-Office Automation
Storing and processing documents such as delivery orders, dock receipts, bills of lading, and sea waybills are time-consuming manual tasks still done mostly by human employees. Robotic process automation (RPA) in the supply chain helps businesses achieve end-to-end document automation using artificial intelligence and OCR. With the right tools and software, tasks like credit, collections, and billing can now be delegated to robots, resulting in a 43% time reduction. This gives human employees more time for problem-solving and brainstorming work.
- Transportation Automation
Despite technical and regulatory challenges, autonomous vehicles remain a promising prospect on the part automation will play in the future of logistics. While automated guided vehicles (AGVs) have been around since the 1950s, their uses are limited to within warehouse premises. Analysts predict that 8 million autonomous vehicles will be shipped in 2025, with uses ranging from autonomous ride-sharing and autonomous shuttles riding along learned paths to self-driving delivery trucks that communicate with other trucks to ensure road safety.
- Warehouse Automation
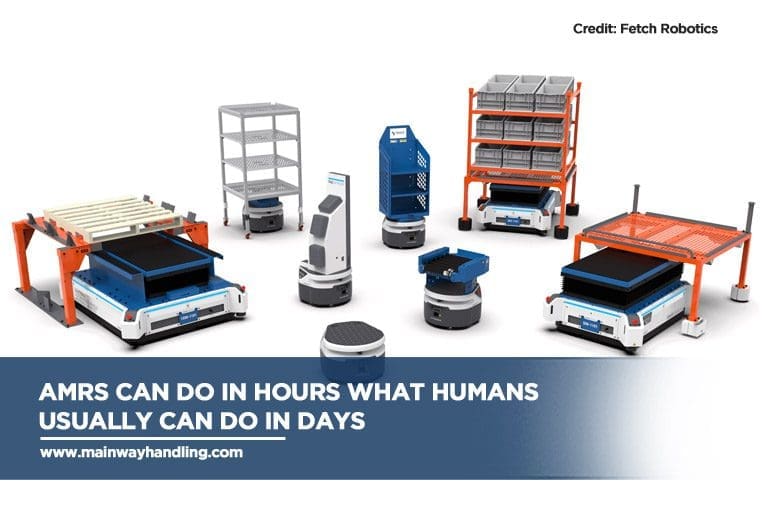
A 2020 Raconteur report reveals that warehouse automation is the top technology invested in by companies across industries aiming to cut delivery times and improve overall margins. Material handling operations run smoothly and efficiently when a warehouse is fully integrated and automated. Applications of warehouse automation include:
AMRs address the limitations of traditional warehouse AGVs, making them better suited to complex warehouse and collaborative activities. They add intelligence, guidance, and sensory awareness to AGVs since they use on-board sensors and processors to autonomously move materials without the need for physical guides or markers. This allows them to operate autonomously, but collaboratively, around humans.


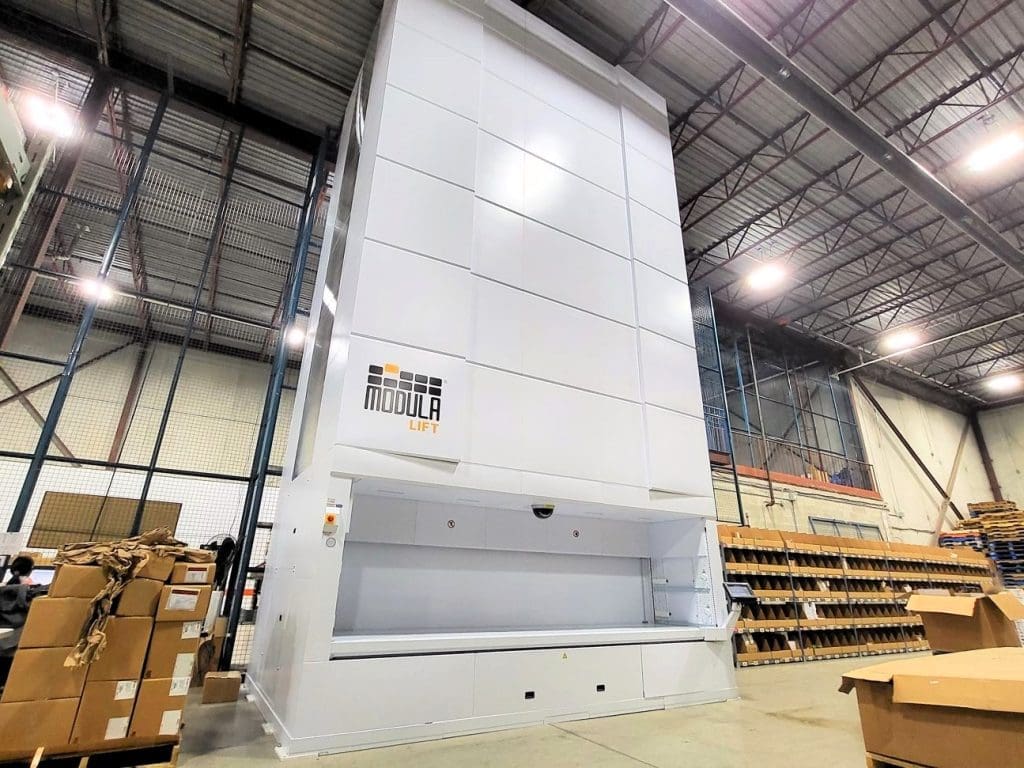
- Collaborative robots
Often referred to as cobots or co-robots, collaborative robots are the newest type of robots designed to interact with people in a shared work environment. Across industries, cobots work side by side with humans in assembly, dispensing, finishing, machine tending, material handling, welding, material removal, quality inspections, and more.
Compared to traditional industrial robots, cobots are teachable and “behave” safely and smartly around humans. Using advanced visual technology and equipped with sophisticated sensors, cobots can detect people within proximity and stop or change their activity as needed.
- Lights-out manufacturers
Lights-out manufacturers operate with little to no human intervention. While extremely rare, there are existing warehouses that fully run on operational automation, defined as a combination of hardware and software that allows a computer installation to run unattended — that is, without the need for a human operator to be physically located at the site of the installation. This is commonly known as automated system operations (ASO). Japanese robotics company FANUC has been operating this way since 2021, while Philips, Ocado, Siemens, and Hirotec are employing a mix of ASO technologies to reduce downtime and increase visibility.
As the go-to automated conveyor system provider, Mainway Handling systems can help these various industries with their specific needs, be it for a warehouse or an automotive business.
How Automation Can Solve Common Supply Chain Problems
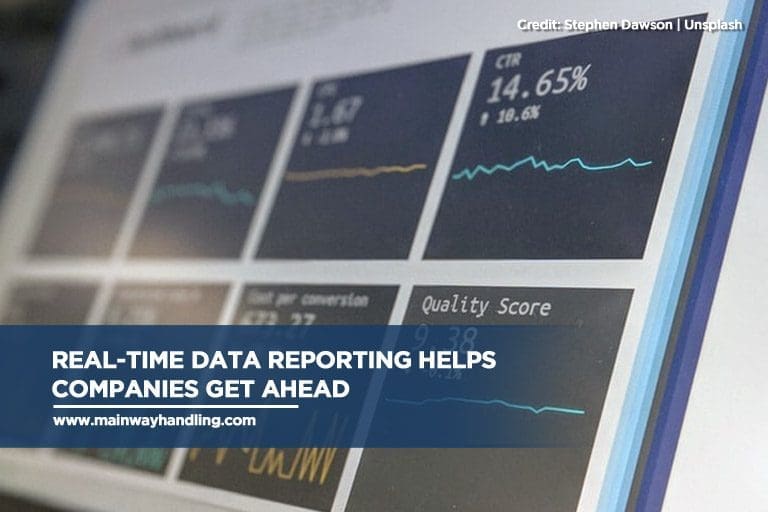
Operating a complex system such as the supply chain guarantees challenges that need to be addressed in a timely manner so the problem doesn’t compromise the whole operation. With the current advances in supply chain automation, common problems can now be addressed by robots designed and programmed to behave specifically in response to that problem.
- Customer Service
Automation expedites order fulfillment processes, which can be tedious when a human employee is assigned to find a product, pick it up, and transfer it to be shipped out. Automated warehouses have begun implementing small pick-and-pack robots that can quickly traverse a warehouse and find the correct object via Stock-keeping Unit (SKU), Universal Product Code (UPC), or even Radio Frequency Identification (RFID). These robots go when they need to go, without having to temporarily leave another task to fulfill another.
A less expensive way to implement automation is providing visibility of the fulfillment process to your customers. This is how they determine the location of their package, when it’s bound to arrive, and any other information they need to keep them in the loop.
- Sudden Difficulties
Power outages, factory fires, or other simpler issues that hinder order fulfillment can damage an entire supply chain. Speed and timeliness are the keys to mitigating any kind of disaster damage. Supply chain automation allows you to put systems into place that will react swiftly to these adverse conditions.
If there is a problem at a manufacturing plant, an automated system could instantly place orders for integral equipment or parts from another provider without the need for the usual pen-and-paper requests that run on a bureaucratic chain of command. Your business saves time, money, and energy, allowing your employees and managers to deal with the human elements of the current problem at hand.
- Growing Shipping Demands
The benefits of logistics automation cannot be overlooked. Employees spend a considerable amount of time figuring out the optimal way to pack a truck, plan the most efficient route, report transit status to clients, and connect the right truckers to the right shipments. Supply chain automation streamlines this process by utilizing logistics AI to figure out and perform all of these tasks, all the while saving you significant delivery costs.
To meet the demands of clients, Mainway Handling Systems has perfected our ability to develop and integrate automation into existing processes. It is our goal to equip you with the right tools to address the aforementioned issues and enhance your manufacturing and distributing framework.
Limitations of Supply Chain Management Automation
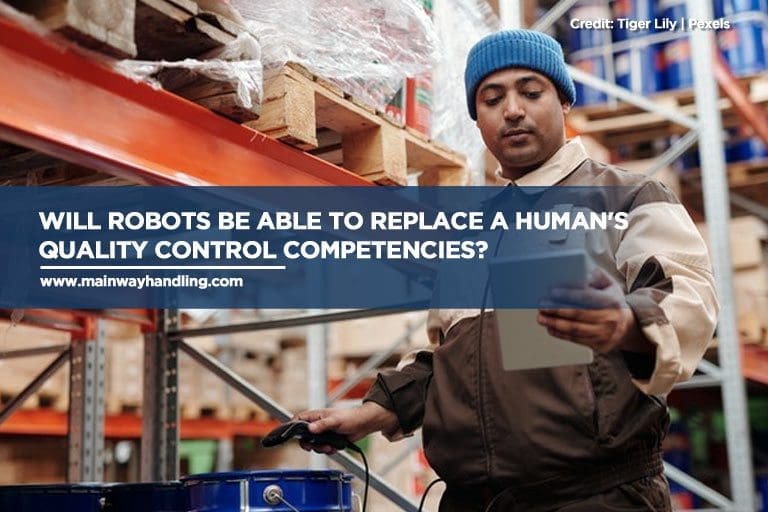
There’s a limit to the power of supply chain automation, which makes the concept of lights-out warehouses still seem like a far-fetched dream. Despite the many advancements in AI and robotics, companies are justified when they remain reluctant on automating most or all of their processes, since:
- Automation lacks the “human touch”
It turns out we cannot completely erase humans out of the picture. Robots were never meant to replace human resources. Instead, we should look at them as complementary assets that perform menial repetitive tasks efficiently so that workers can attend to higher-level tasks such as:
- brainstorming
- complex problem solving and decision-making
- planning and management
- personal relations and human resources
- sales talk
The Economist Intelligence Unit (EIU) reports that firms recognize the need for greater technical skills in their workforces in order to successfully digitize their supply chains. A third of the surveyed executives report that an understanding of business strategy and operations, the ability to communicate effectively, and digital savviness are the most important skills for a supply-chain executive of the future. These competencies cannot be easily programmed into robots and artificial intelligence without a huge risk for errors.
- Automation comes with a hefty price tag
The slow adoption of automation can be attributed to the costs of AI, robotics, and other forms of automation:
- A single industrial robot costs around $50,000 to $80,000, and with the addition of application-specific peripherals, may total $100,000 to $150,000 PER UNIT.
- IT and corporate businesses, despite the nature of their work, are reluctant to apply AI to their systems. A survey by MarketMuse reveals that more than 50% of these businesses have concerns about total costs of implementation, the impact of these costs on current expenditure levels, and how to measure the ROI of a new AI solution.
Founder and president of LMA Consulting Group Inc., Lisa Anderson, finds this reluctance among companies justifiable. She states, “Most executives do not want to be the guinea pig for new technology as they cannot afford disruption and risk. Thus, as new technologies such as robotization and AI advance, they are starting to put their toe in the water to test these technologies and partner with experts to find ways to utilize these technologies to achieve bottom-line improvements.“
Supply chain executives await more cost-related data, as well as proof of the effectiveness of these automated solutions before they jump in and make a significant investment. Once an accurate ROI for such an undertaking is available, supply chain automation adoption rates are expected to rise in the next 5 years.
Embracing Supply Chain Technology to Get Ahead of the Game

Global research giant Gartner predicts that the next 3 to 5 years will see an increase in digital supply chain technologies, amplified by the pandemic and the need for social distancing and the flux of global e-commerce. This will compel supply chain leaders to integrate IT-focused roles for their human resources, as well as heavier investments in advanced AI and analytics.
Two key points focus on how automation will help shape the future of supply chains:
- By 2023, demand for robotic goods-to-person (G2P) systems will have quadrupled to help enforce social distancing in warehouses.
Gartner VP analyst Dwight Klappich sees the adoption of robotic G2P systems to benefit warehouse operators even long after the pandemic is gone. Besides addressing the present need for social distancing in warehouse operations, robotic G2P is seen to improve storage density and increase productivity, as the technology is advanced, economical, and customizable to every kind of warehouse environment.
- By 2024, 50% of supply chain organizations will have invested in applications that support artificial intelligence and advanced analytics capabilities.
Despite the limitations of automation, companies are expected to adopt some form of automation to improve their processes and make faster, more informed decisions. These needs were further amplified by the COVID-19 pandemic and the disruptions supply chains across the world had to endure.
Leading supply chain organizations now employ AI and advanced analytics to be in the know of their business and their industry as a whole, as well as try to predict what might happen in the future. More companies are expected to catch on, and they must adopt a broad and holistic perspective in applying data mining, visibility tools, transport automation, and other capabilities to reach specific strategic objectives.
Warehouse Automation for Crisis-Proof Operations
Mainway Handling Systems specializes in autonomous robotics, automated solutions, and conveyor systems. We help you integrate a modular, adaptable, and efficient sortation system or distribution center in your warehouse. Email at sales@mainwayhandling.com, or call (905) 335 0133 now!
Comments are closed